Project Description
Key information
Project title: Next-generation coatings for advanced wear-resistant materials
Project in the Spotlight: N19016
Funding: HTSM2019
Partners: Tata Steel, SKF, Wuppermann
Run time: November 2020-March 2025
Market: Automotive
Written by M2i Program Manager: Jeroen van Beeck
The research project
The project addressed the limitations of Zn-based corrosion protection coatings which are widely used in the industry. These coatings often exhibit poor damage and wear resistance, leading to surface defects in formed parts. The research focused on unravelling the micro-mechanics of these coatings and develop guidelines for designing the next-generation coatings with improved performance. A synergistic experimental-numerical approach was employed, investigating the atomic-scale mechanisms governing plasticity, damage, and wear in zinc-containing alloys. This combined experimental-numerical approach, allowed the researchers to identify key atomic-scale mechanisms.
Consortium
The research project benefited from the collaboration of a strong consortium comprising academic and industrial partners, each contributing unique expertise and resources. The academic partners, University of Groningen and Eindhoven University of Technology, brought in-depth knowledge of atomistic and continuum scale modeling, as well as extensive experience in multi-scale mechanical testing and microscopy techniques. This expertise was complemented by the industrial partners, Tata Steel, SKF, and Wuppermann Staal Nederland. They provided practical insights into the production and application of coating materials, as well as access to real-world testing environments and materials. The combined strengths of the consortium members ensured the practical relevance and applicability of the research outcomes.
Exemplary results
Atomistic simulations
Simulation work performed at the University of Groningen unraveled the atomistic mechanisms that control plastic deformation of Zn-based coatings. Zn is an extremely anisotropic metal, that tends to be brittle because only a few slip systems (basal) get activated. However, hexagonal-closed-packed (HCP) crystals like zinc can potentially activate a large number of slip and twinning system, by alloying. In this project, we developed a framework that enables to predict multiple slip activation by scanning through the entire periodic table. This framework will be instrumental to guide industry in finding new wear-resistant Zn-alloy coatings.
Experimental studies
Nano- and micromechanical experiments performed at the Eindhoven University of Technology shed light on the complex interaction among multiple plastic deformation mechanisms in zinc coatings, including dislocation glide, twinning and grain boundary sliding. The understanding of the complex interplay among these mechanisms created a spark to finally resolve a long lasting wear problem in industry and will be deepened in future experiments.
Industrial application
Next-Coat has provided deep insights in the highly anisotropic micro-mechanical behavior of Zn-based coatings, which opened new product development opportunities at Tata Steel, SKF and Wupperman. At Tata Steel the results from the micro-scale experimental studies directly feed into process optimizations to make the coating more wear resistant in deep-drawing applications. The atomistic simulations have brought attention to specific coating alloying elements for new coating chemistries which will be further developed in the coming years.
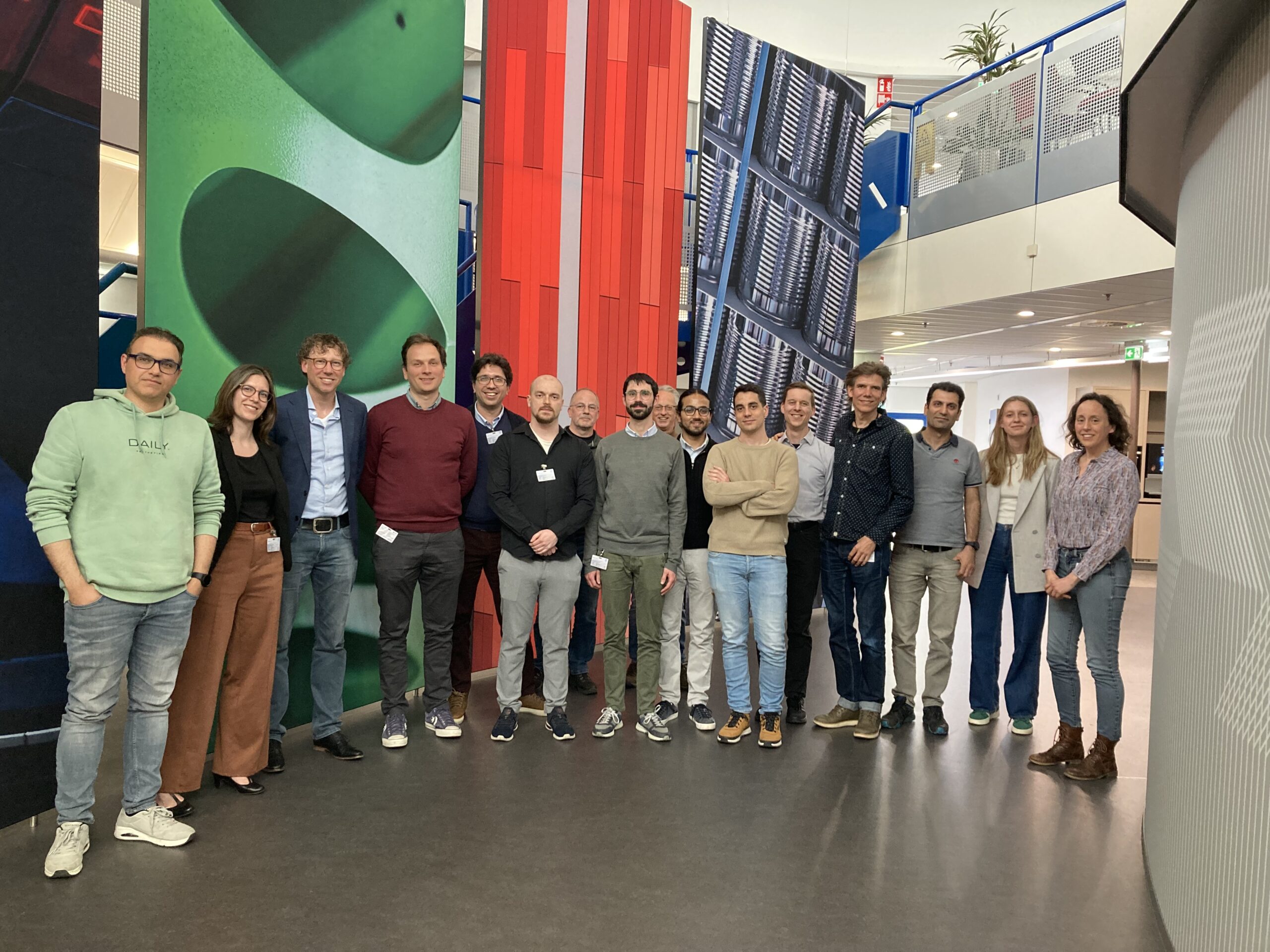
Pieter Baart, Principal Scientist Tata Steel Nederland Technology
“The in-depth technical discussions with the project team changed our view on our coatings. Next-Coat provided us with valuable tools and directions to improve our coatings which enables further improvement in product surface quality and process efficiency at our customers. It was very inspiring to work in the highly dedicated Next-Coat team.”
Dennis König, PhD researcher of Next-Coat at the Eindhoven University of Technology
“Within the framework of the Next-Coat project, I investigated the deformation behavior of zinc grains extracted from coatings, which provided a foundation for in-situ studies of the coatings under tensile stress. Additionally, we developed a novel setup to study the galling behavior of zinc-based coatings within a scanning electron microscope (SEM). Collaborating with industry partners and the University of Groningen significantly contributed to enhancing the outcomes of the project.”
Francesco Maresca, Next-Coat Project Leader and Associate professor at University of Groningen
“Within Next-Coat, we investigated, together with the Eindhoven University of Technology, the complex deformation behavior of Zinc-based coatings. By leveraging our multi-scale expertise and a strong numerical/experimental synergy, we shed light on plasticity mechanisms at the nano- and micro-scales, by means of state-of-the-art atomistic and crystal plasticity simulations coupled to experiments results from Eindhoven. The insight gathered in the project has created a base for further development of these coatings.”