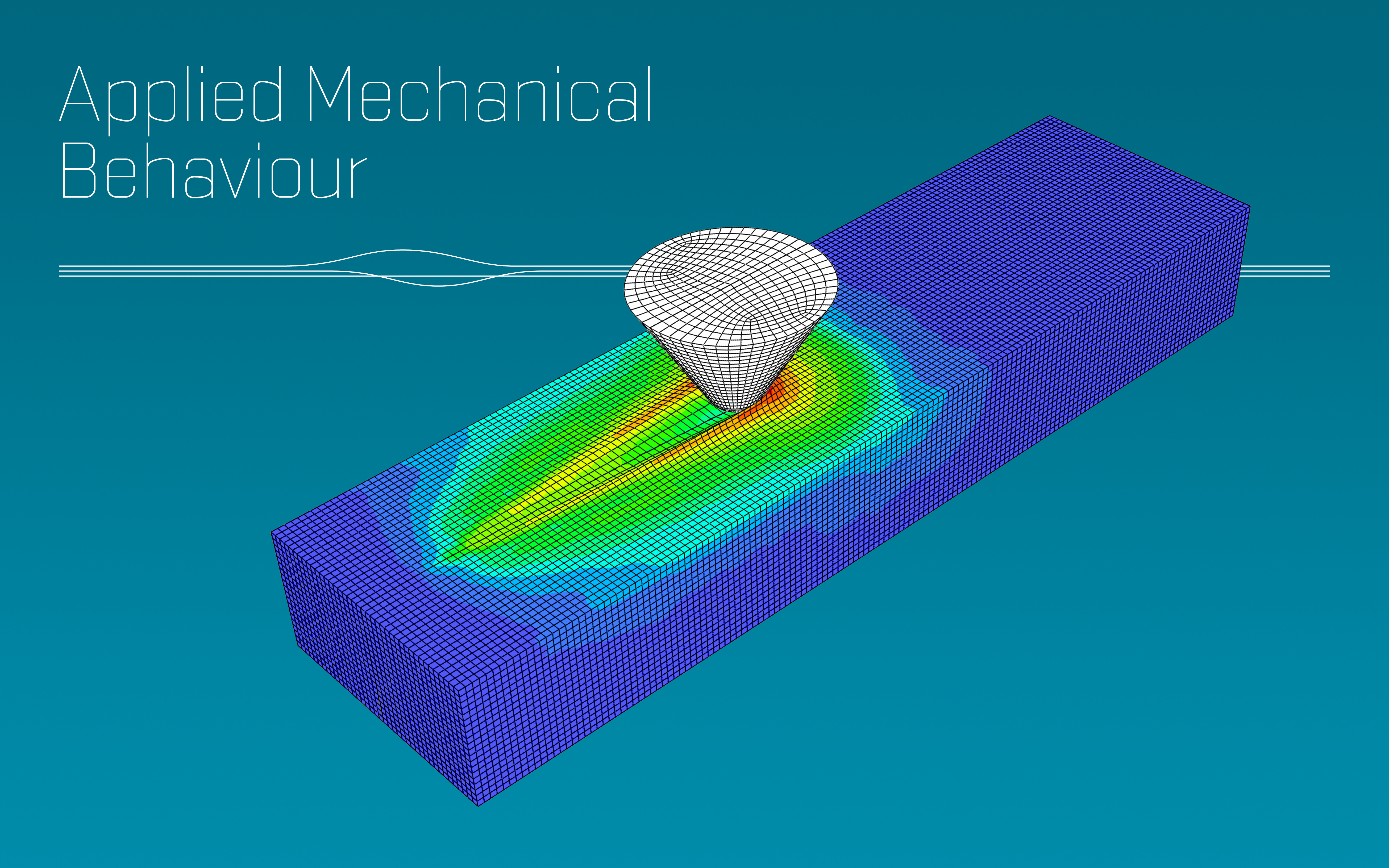
M2i’s Applied Mechanical Behaviour Cluster aims to improve numerical modelling techniques for the simulation of production processes and product performance in relation to material behaviour. Modelling is an essential enabling technology for several market segments, resulting in a reduction of the number of trial-and-error cycles and thus faster time to market, reduction of rejected parts and improved product quality.
Failure analysis in wall ironing of cans and batteries
With the steep rise in sales of electrical vehicles the demand for batteries is increasing rapidly. One of the battery technologies, as for example used by Tesla, is to build the battery pack from cylindrical cells, which are made using established battery casing technology. The battery casing (the so-called battery can) is typically manufactured from steel. During drawing so-called earing occurs, which must be trimmed, and thus material is lost, i.e. waste is generated. The aim of the current project is to create a model to establish for a given tooling geometry what amount of planar anisotropy can be tolerated in the sheet material. And vice versa, given a certain amount of planar anisotropy, which tooling design will allow for a robust battery can manufacturing process.
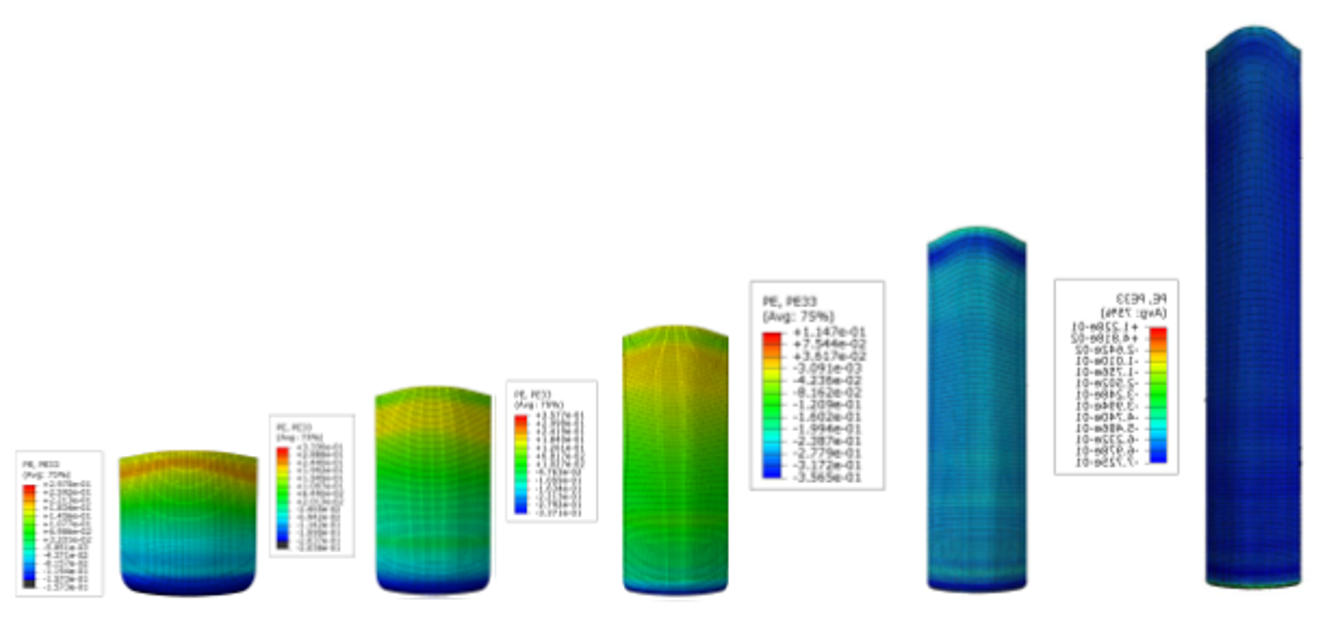
Grease Life Prognostics: Remaining Grease Life Estimation by Measuring Grease Properties and Using Predictive Models
Bearings are the most widespread machine elements after nuts and bolts. Some 80-90% of these are grease lubricated. The application of grease may in some cases be limited due to its finite life. For many bearing applications, this results in setting up fixed maintenance schedules. In railway bearings, for instance, grease is refreshed at regular intervals. These intervals have been determined on the basis of experience rather than real grease conditions. Having an accurate grease life model will make the operation of bearings, such as railway bearings (but also in a large range of other machinery) much more efficient and economical. Next to that, there is an environmental impact to consider as used grease cannot be re-used. Tailoring the maintenance intervals will make the use of grease more resource efficient leading to less disposal of used grease. The aim of this project is to determine the end of grease life by monitoring its yield stress and oil content and extrapolating them to their critical values using a reliable model describing their evolution. Evidently, this would be of great industrial value since this straightforwardly enables predictive maintenance.
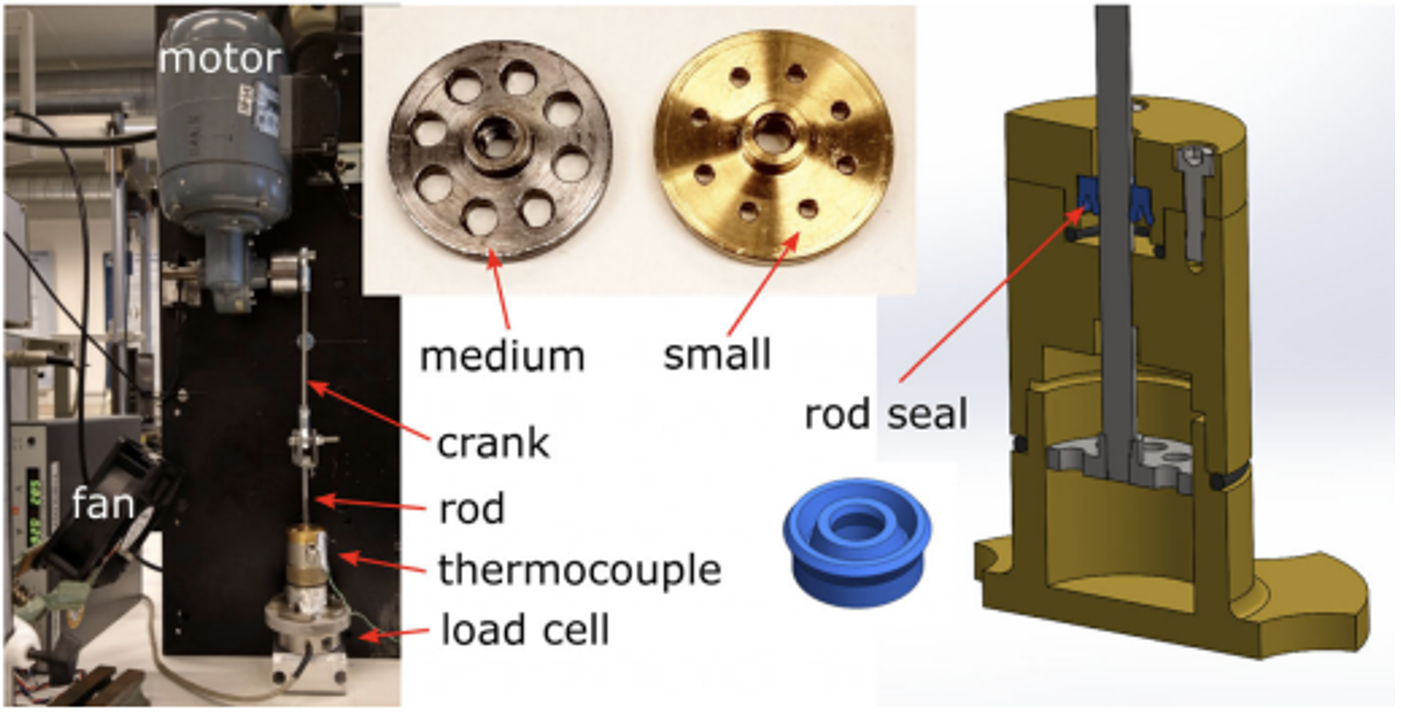
More information
For more information about our Applied Mechanical Behaviour Cluster, please contact Jeroen van Beeck.